Fly Ash Bricks Project Report
Fly Ash Bricks Project Report: A Complete Guide
Introduction
Fly ash bricks are an eco-friendly alternative to traditional clay bricks, made from the by-products of coal combustion in thermal power plants. Due to their durability, strength, and sustainability, fly ash bricks have become an increasingly popular choice in the construction industry. These bricks are cost-effective, consume less energy during manufacturing, and help reduce carbon emissions.
In this project report, we will discuss the step-by-step process of setting up a fly ash bricks manufacturing plant, including cost analysis, equipment, raw materials, labor requirements, and marketing strategies. This report is designed for entrepreneurs looking to establish a fly ash brick-making business and contribute to the sustainable building materials sector.
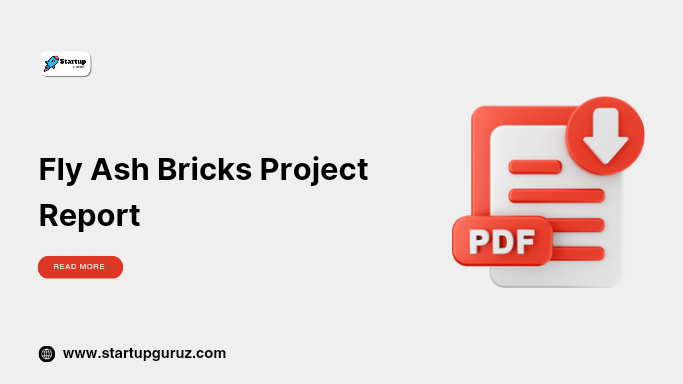
Market Analysis
1. Overview of the Fly Ash Brick Industry
The construction industry is growing rapidly, leading to increased demand for building materials like bricks. Fly ash bricks have gained significant attention due to their sustainability, strength, and thermal insulation properties. These bricks are a by-product of coal combustion in power plants, which makes their production not only cost-effective but also environmentally friendly. Governments and environmental agencies are also promoting the use of fly ash bricks as part of sustainable construction practices.
2. Target Market
The target market for fly ash bricks includes:
- Construction companies: These companies use bricks in building projects, particularly those focused on green building practices.
- Real estate developers: Real estate developers are increasingly shifting toward sustainable materials, making fly ash bricks a preferred choice.
- Local brick dealers: Local dealers distribute fly ash bricks to small builders and construction workers for use in residential and commercial projects.
- Government projects: Fly ash bricks are used in public infrastructure projects such as roads, schools, and government buildings.
Why Fly Ash Bricks?
1. Eco-Friendly and Sustainable
Fly ash is a waste material from thermal power plants. By using this waste product in brick manufacturing, businesses can help reduce the harmful environmental impact of coal combustion. Traditional clay bricks involve soil depletion and high energy consumption during production, while fly ash bricks help conserve natural resources.
2. High Durability and Strength
Fly ash bricks have high compressive strength, making them suitable for load-bearing construction. They also have lower water absorption rates, which improves the structure’s longevity and reduces the likelihood of cracks.
3. Cost-Effective
The production of fly ash bricks is more economical than that of clay bricks because of the availability of fly ash as a by-product. This cost advantage is passed on to consumers, making these bricks an affordable choice for builders.
4. Thermal Insulation
Fly ash bricks offer excellent thermal insulation, keeping buildings cooler in hot climates and reducing energy consumption for air conditioning.
Raw Materials and Equipment Required
1. Raw Materials for Fly Ash Bricks
The key raw materials for producing fly ash bricks include:
- Fly Ash: Sourced from thermal power plants.
- Sand: Added to the mix to enhance texture.
- Cement or Lime: Used as a binding material.
- Gypsum: Enhances the quality and strength of the bricks.
- Water: Used to mix and mold the bricks.
2. Equipment Needed for Manufacturing
Setting up a fly ash brick manufacturing unit requires the following machinery:
- Fly Ash Brick Making Machine: Semi-automatic or fully automatic machines are available in the market, capable of producing a large number of bricks daily.
- Pan Mixer: Used for mixing the raw materials thoroughly.
- Hydraulic Press: For shaping and compressing the fly ash mixture into brick molds.
- Conveyor Belts: To transport raw materials from one machine to another.
- Curing Chambers: To allow bricks to cure in a controlled environment for better quality and strength.
Manufacturing Process of Fly Ash Bricks
The production of fly ash bricks involves several stages, which include:
1. Collection of Raw Materials
The primary raw materials (fly ash, sand, gypsum, and cement or lime) are collected from reliable sources, preferably located close to the manufacturing unit to reduce transportation costs.
2. Mixing
The collected raw materials are mixed thoroughly using a pan mixer. The fly ash is blended with sand, gypsum, and cement in precise ratios to form a homogenous mixture.
3. Molding
The mixed material is fed into a hydraulic press machine where it is compressed into the desired brick shape. The hydraulic press applies a significant amount of pressure, ensuring the bricks are strong and well-shaped.
4. Curing
After molding, the bricks are cured either in the open air or in curing chambers. Curing improves the bricks’ compressive strength and ensures they attain the necessary hardness. Curing can take anywhere from 7 to 28 days, depending on the required quality.
5. Quality Testing
The bricks undergo quality tests such as compressive strength, water absorption, and dimension checks to ensure they meet industry standards. Once they pass all tests, they are ready for packaging and distribution.
Cost Analysis and Financial Projections
1. Initial Setup Costs
The setup cost for a fly ash bricks manufacturing unit depends on factors like location, machinery type, and the scale of operations. A basic breakdown of the costs is as follows:
- Land and Building: ₹10,00,000 to ₹15,00,000 (depending on the location and size of the plant).
- Machinery: ₹15,00,000 to ₹25,00,000 (for semi-automatic or fully automatic machines).
- Raw Materials (Initial Stock): ₹2,00,000 to ₹3,00,000 (fly ash, sand, cement, gypsum).
- Labor Costs: ₹1,00,000 to ₹1,50,000 per month (depending on the number of workers).
- Miscellaneous Costs: ₹2,00,000 (utilities, transportation, maintenance).
Total Initial Investment: ₹30,00,000 to ₹45,00,000
2. Recurring Expenses
- Raw Materials: ₹1,00,000 to ₹2,00,000 per month.
- Labor: ₹1,00,000 to ₹1,50,000 per month.
- Utilities (Electricity, Water): ₹10,000 to ₹15,000 per month.
- Maintenance: ₹10,000 per month.
Total Monthly Expenses: ₹2,20,000 to ₹3,00,000
3. Revenue and Profit Margins
A small fly ash brick unit can produce approximately 50,000 to 75,000 bricks per month. If each brick sells for ₹5 to ₹6, the total monthly revenue can range from ₹2,50,000 to ₹4,50,000.
After deducting monthly expenses, the expected monthly profit is between ₹50,000 and ₹1,50,000. Profit margins will increase as production capacity and market demand grow.
Marketing Strategy
1. Direct Selling to Construction Companies
Reach out to local construction companies and developers that prefer eco-friendly building materials. Building long-term relationships with construction firms can lead to consistent sales.
2. Tie-Ups with Real Estate Developers
Collaborating with real estate developers who focus on sustainable building practices can ensure bulk orders and a steady revenue stream.
3. Local Dealers
Partner with local brick dealers who distribute bricks to small builders, contractors, and individual homeowners. Offering competitive prices and bulk discounts can help increase sales through local distributors.
4. Government Tenders
Participating in government tenders for construction projects that prioritize eco-friendly materials can provide significant opportunities for growth. Many public infrastructure projects use fly ash bricks to promote sustainability.
Sustainability and Environmental Impact
Fly ash bricks contribute to sustainable development by utilizing waste material from thermal power plants that would otherwise be disposed of in landfills, causing environmental harm. These bricks also require less energy to manufacture compared to traditional clay bricks, reducing carbon emissions.
Moreover, using fly ash bricks helps preserve topsoil, which is extensively used in clay brick manufacturing. By opting for fly ash bricks, the construction industry can significantly reduce its environmental footprint.
FAQs about Fly Ash Bricks
- What are the raw materials used in fly ash brick production?
Fly ash, sand, cement or lime, gypsum, and water are the main raw materials used in manufacturing fly ash bricks. - How much does it cost to set up a fly ash brick manufacturing plant?
The setup cost ranges from ₹30,00,000 to ₹45,00,000, depending on location, scale, and machinery type. - What are the benefits of using fly ash bricks over traditional clay bricks?
Fly ash bricks are more durable, cost-effective, eco-friendly, and offer better thermal insulation compared to traditional clay bricks. - How many bricks can a small fly ash brick unit produce per day?
A small unit can produce around 2,000 to 3,000 bricks per day, depending on the capacity of the machinery. - What is the market price of fly ash bricks?
Fly ash bricks are typically sold at ₹5 to ₹6 per brick, depending on quality and region. - Is there government support available for fly ash brick manufacturers?
Yes, various state and central government schemes provide subsidies and incentives for eco-friendly businesses like fly ash brick manufacturing. - How long does it take to cure fly ash bricks?
Curing takes about 7 to 28 days, depending on the type of bricks and environmental conditions. - What is the compressive strength of fly ash bricks?
Fly ash bricks typically have a compressive strength of 7.5 to 10 MPa, making them stronger than clay bricks. - Can fly ash bricks be used for load-bearing walls?
Yes, fly ash bricks are suitable for both load-bearing and non-load-bearing walls due to their high compressive strength. - Are fly ash bricks environmentally friendly?
Yes, fly ash bricks are eco-friendly as they use industrial waste (fly ash), reduce soil erosion, and emit fewer pollutants during production.
Conclusion
Fly ash bricks represent an opportunity for entrepreneurs to enter the booming construction industry with a sustainable and cost-effective product. With increasing demand for eco-friendly building materials, the market for fly ash bricks is set to grow. By investing in the right machinery, raw materials, and marketing strategies, you can build a profitable business while contributing to environmental conservation.