Mini Flour Mill Project Report
Mini Flour Mill Project Report
Setting up a mini flour mill can be a lucrative venture, especially as demand for fresh, quality flour continues to rise. Flour is a daily staple for households, bakeries, and food industries, which has led to an increase in small-scale milling businesses. This guide provides an in-depth mini flour mill project report that outlines the essentials of starting a flour mill, including setup requirements, cost estimation, machinery, licenses, and a comprehensive financial plan.
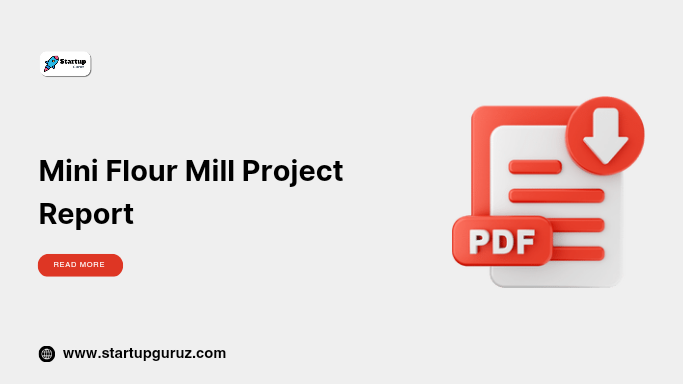
Mini Flour Mill Project Report Outline
- Introduction
- Importance of a Mini Flour Mill Project Report
- Business Model Overview
- Market Analysis
- Machinery and Equipment
- Cost Estimation and Financial Plan
- Location and Infrastructure Requirements
- Licensing and Legal Requirements
- Risk Assessment and Management
- FAQs
1. Introduction
The purpose of a mini flour mill project report is to provide a roadmap for setting up a small-scale flour mill. It includes all necessary details for the entrepreneur to understand costs, equipment requirements, market potential, and operational plans. A project report is also essential when applying for loans or presenting the business to investors.
2. Importance of a Mini Flour Mill Project Report
- Financial Clarity: Outlines the capital and operational costs, aiding in budget planning.
- Market Insight: Highlights demand trends, enabling market-oriented production.
- Risk Mitigation: Identifies potential risks and their solutions.
- Investment Attraction: A clear project report increases investor confidence.
- Strategic Planning: Serves as a blueprint for setting up and running the mill efficiently.
3. Business Model Overview
- Type of Flour: The mini mill typically produces wheat flour, maize flour, or other grains, depending on local demand.
- Product Range: Whole wheat flour (atta), refined flour (maida), semolina (suji), and bran are common products.
- Revenue Sources: Income from packaged retail flour, bulk supply to bakeries, and local distributors.
- Distribution Channels: Sales through local retail shops, bakeries, wholesalers, and direct consumers.
- Target Market: Residential areas, grocery stores, small restaurants, and bakeries.
4. Market Analysis
Market Demand and Opportunity
- Growing Demand: With rising population and increased health awareness, there is significant demand for fresh, quality flour.
- Local Competition: Analyze competitors in the area and identify your unique selling points.
- Consumption Trends: Many consumers prefer locally milled flour for its freshness and quality.
- Growth Potential: As small bakeries and eateries expand, demand for local flour mills increases.
Competitor Analysis
- Small-Scale Mills: Assess the quality, pricing, and service of local competitors.
- Larger Mills: Understand the branding strategies of larger flour mills and their customer base.
- Pricing Strategy: Position yourself competitively to capture both retail and wholesale customers.
5. Machinery and Equipment
Setting up a mini flour mill requires various types of machinery, including:
- Cleaning Machine: To remove stones, dirt, and impurities from raw grain.
- Grinding Machine: To grind the grains into flour.
- Separator: Separates different grades of flour and bran.
- Packing Machine: For packaging flour in various weights.
- Quality Control Equipment: To ensure consistency in flour texture and quality.
Cost of Machinery
The machinery cost for a small-scale flour mill is around ₹3-5 lakh, depending on production capacity.
6. Cost Estimation and Financial Plan
Initial Setup Costs
- Land and Building: For a small plant, around ₹1-2 lakh if rented; purchasing land will vary by location.
- Machinery and Equipment: Basic machinery setup costs approximately ₹3-5 lakh.
- Licensing and Permits: Around ₹20,000-50,000, covering all necessary legal permissions.
- Raw Materials: Wheat or other grains based on local consumption trends.
Operational Costs
- Labor: Skilled and unskilled workers with monthly wages around ₹20,000-50,000.
- Utilities: Electricity, water, and maintenance costs for machinery.
- Packaging and Marketing: Packaging material and local advertising costs.
- Miscellaneous Costs: Transportation, equipment repair, and other expenses.
Revenue and Profitability
Expected revenue depends on production capacity and local demand. For example, a mini flour mill with a daily output of 500 kg can reach profitability within 2 years if properly managed.
7. Location and Infrastructure Requirements
Selecting a good location helps reduce costs and streamline operations:
- Accessibility: Choose a location accessible to raw materials and target markets.
- Space: A mini flour mill requires around 800-1500 square feet for storage, milling, and packaging.
- Utilities: Stable access to electricity and water.
- Proximity to Market: Being closer to the target market reduces logistics costs and enhances product freshness.
8. Licensing and Legal Requirements
To operate a mini flour mill legally, you must acquire the following:
- FSSAI License: Mandatory for food processing businesses to ensure safety standards.
- GST Registration: Required for tax purposes.
- Trade License: Permission to operate within local jurisdiction.
- BIS Certification: Optional, but recommended to establish product credibility.
- Pollution Control Clearance: Check local regulations for waste management and noise control.
9. Risk Assessment and Management
Understanding potential risks allows for better business planning:
- Supply Chain Risks: Secure reliable suppliers for raw grains to avoid shortages.
- Market Risks: Fluctuations in demand and consumer preferences.
- Operational Risks: Equipment breakdowns or power outages; schedule regular maintenance.
- Financial Risks: Inadequate working capital; maintain a cash reserve for unforeseen expenses.
FAQs on Mini Flour Mill Project Report
- What is the cost to set up a mini flour mill?
The setup cost ranges from ₹5-10 lakh, depending on the location, capacity, and equipment. - How much space is required for a mini flour mill?
A small flour mill requires around 800-1500 square feet for storage, milling, and packaging. - What is the average production capacity of a mini flour mill?
Small mills can produce 500-2000 kg of flour per day, depending on machinery and manpower. - Is a mini flour mill profitable?
Yes, mini flour mills can achieve profitability within 2-3 years with efficient operations and local demand. - What type of flour can be produced in a mini mill?
Whole wheat flour, refined flour, semolina, and bran are common products. - What licenses are required for a mini flour mill?
An FSSAI license, GST registration, trade license, and pollution control certificate are essential. - How can I market a mini flour mill?
Market through local grocery stores, small restaurants, and direct-to-consumer packaging. - Can I expand my mini flour mill in the future?
Yes, additional machinery can be purchased to increase production capacity as demand grows. - How much labor is required?
Typically, 4-5 skilled and unskilled workers are needed to operate a small mill. - Are there eco-friendly practices for a mini flour mill?
Yes, by using recyclable packaging and minimizing water waste, the operation can be made sustainable.
Conclusion
A mini flour mill project report is essential for any entrepreneur looking to enter the flour milling industry. With growing demand for fresh flour, a mini flour mill presents a profitable business opportunity. This report provides a detailed framework for setting up the mill, estimating costs, and planning for long-term growth. It serves as a guide to understand the legal, financial, and operational aspects, making it easier to start and manage the business effectively.