Sugar Factory Project Report
Sugar Factory Project Report
Introduction
The sugar industry plays a critical role in many economies, especially in countries with high sugarcane cultivation. Sugar is a versatile commodity with applications in food, beverages, and various industrial products. A sugar factory processes raw sugarcane into refined sugar, molasses, and by-products that are further used in different industries. Given the strong demand for sugar and its by-products, setting up a sugar factory can be a profitable business venture.
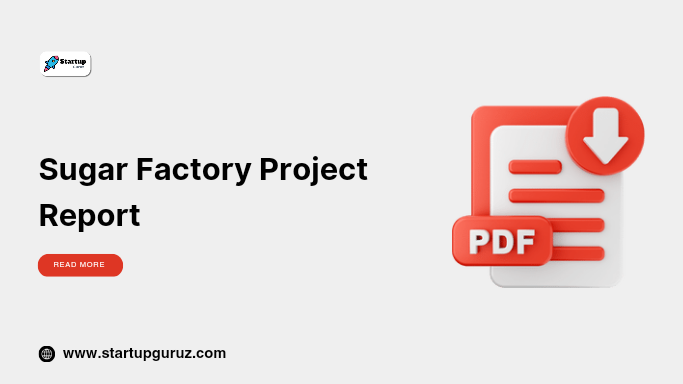
Benefits of Setting Up a Sugar Factory
- Consistent Demand: Sugar is a staple food product with constant demand.
- Diverse Revenue Streams: Producing by-products like molasses, ethanol, and bagasse opens additional revenue opportunities.
- Employment Generation: Sugar factories create jobs in rural areas and contribute to economic growth.
- Agricultural Support: Encourages local sugarcane farmers, providing them with a stable market.
- Export Potential: Many countries rely on sugar imports, making exports a viable revenue stream for sugar factories.
Project Report Structure for a Sugar Factory
This sugar factory project report will cover the following sections:
- Executive Summary
- Project Objectives
- Market Analysis
- Location and Infrastructure Requirements
- Machinery and Equipment
- Financial Planning and Cost Estimation
- Licenses and Permits
- Environmental Impact
- Risk Management
- FAQs
1. Executive Summary
The executive summary offers a concise overview of the sugar factory project:
- Project: Establishment of a sugar manufacturing plant with a defined production capacity.
- Target Market: Local, national, and international food and beverage markets.
- Location: Proximity to sugarcane sources to reduce transportation costs and enhance efficiency.
- Goals: To provide high-quality sugar, generate employment, and contribute to economic development.
2. Project Objectives
The main objectives of the sugar factory project are:
- Sustainable Sugar Production: Establish a factory with efficient production and minimum waste.
- Local Economic Growth: Support sugarcane farmers with a reliable buyer.
- Profitability: Ensure steady returns on investment through effective management and production.
- Environmental Responsibility: Use eco-friendly methods and equipment to reduce environmental impact.
3. Market Analysis
Sugar demand is driven by the food and beverage industry, which accounts for the largest consumption. Factors influencing market demand include:
- Rising Population and Urbanization: More people and growing urban areas increase sugar consumption.
- Health Trends: Increasing awareness of sugar’s impact on health may influence the demand for refined versus natural sugars.
- Exports: Sugar has a steady demand in the international market, especially in countries with low domestic production.
Competitor Analysis
Identify local and international competitors and assess:
- Pricing: Analyze prevailing sugar prices to set competitive pricing.
- Distribution Channels: Investigate channels used by competitors for effective market reach.
- Product Differentiation: Offer unique products, such as organic sugar or low-glycemic options.
Pricing Strategy
Develop pricing that reflects:
- Production Costs: Include costs for raw materials, labor, and utilities.
- Market Conditions: Position prices to remain competitive without sacrificing profitability.
- Profit Margins: Aim for sustainable margins that support growth and reinvestment.
4. Location and Infrastructure Requirements
Choosing a strategic location is essential for cost-effective production and distribution:
- Proximity to Sugarcane Fields: A location close to sugarcane sources reduces transportation costs.
- Good Transportation Access: Easy access to transportation for raw materials and product distribution.
- Space Requirements: A typical sugar factory requires 10,000–20,000 square feet, including storage, processing, and packaging areas.
5. Machinery and Equipment Needed
Setting up a sugar factory involves specialized machinery and equipment, including:
- Sugarcane Crusher: For extracting juice from sugarcane.
- Boilers and Vacuum Pans: To evaporate water and crystallize sugar.
- Centrifugals: Separate crystals from molasses.
- Dryers and Coolers: For drying and cooling sugar crystals before packaging.
- Packaging Equipment: Machines for automated packaging.
- Quality Control Systems: Equipment to monitor sugar quality, purity, and safety.
6. Financial Planning and Cost Estimation
Setting up a sugar factory requires significant capital investment. Below is a breakdown of cost estimates:
Initial Setup Costs
- Land and Building: Depending on location, purchasing land and construction can cost between ₹10–20 lakh.
- Machinery and Equipment: Machinery can cost around ₹50-80 lakh, depending on capacity.
- Raw Materials: Sugarcane procurement costs vary based on market prices.
- Licenses and Permits: Licensing costs range from ₹1–3 lakh, depending on regulations.
Operating Costs
- Labor: Skilled labor is required to manage equipment and production, costing ₹2-5 lakh per month.
- Utilities: Costs for electricity, water, and boiler fuel.
- Transportation: Cost of transporting sugarcane to the factory and finished sugar to distributors.
- Maintenance and Repair: Regular maintenance of machinery to avoid breakdowns.
Profitability Calculation
A medium-capacity factory can generate monthly revenue of ₹50-75 lakh, with monthly operational costs between ₹30-40 lakh, resulting in an estimated profit margin of 20-30%. A well-managed factory can achieve payback in about 3-5 years.
7. Licenses and Permits
Operating a sugar factory requires various licenses to comply with industry standards:
- Food Safety License: Ensures food safety standards are met.
- Pollution Control Clearance: Compliance with environmental regulations for waste management.
- Factory License: Required to operate an industrial facility.
- Trade License: Allows lawful business operation within the region.
8. Environmental Impact
Sugar factories must be mindful of environmental impact, particularly waste management:
- Efficient Water Usage: Use water recycling systems to reduce water waste.
- Waste Management: Use by-products like bagasse for biofuel and molasses for ethanol production.
- Pollution Control: Install filters and scrubbers to minimize air pollution from boilers.
9. Risk Management
Key risks to address include:
- Supply Chain Risks: Secure agreements with sugarcane suppliers to avoid raw material shortages.
- Market Fluctuations: Maintain a financial buffer to manage price changes in sugar.
- Operational Risks: Ensure regular maintenance and skilled personnel to avoid production delays.
- Compliance Risks: Regularly update practices to meet new government regulations.
FAQs on Sugar Factory Project
- What is the estimated cost to set up a sugar factory?
Initial setup costs range from ₹1-2 crore, depending on capacity and location. - How much land is needed for a sugar factory?
A medium-scale sugar factory requires 10,000-20,000 square feet of space. - What licenses are required for a sugar factory?
Licenses include food safety, pollution control, factory license, and trade license. - How long does it take to become profitable?
Most sugar factories achieve profitability within 3-5 years. - What is the typical production process in a sugar factory?
Sugarcane is crushed, juice is purified, boiled, crystallized, and then centrifuged to produce refined sugar. - Are there environmental concerns for sugar factories?
Yes, managing waste and emissions is crucial, requiring compliance with pollution control regulations. - Can sugar by-products be used for additional revenue?
Yes, by-products like molasses and bagasse are used to produce ethanol and biofuels. - What is the ideal location for a sugar factory?
Near sugarcane farms to minimize transportation costs. - How can a sugar factory reduce operational costs?
Optimizing water use, recycling by-products, and regular equipment maintenance can reduce costs. - What are common distribution methods for sugar products?
Distribution includes retail, bulk sales to food industries, and export to international markets.
Conclusion
Establishing a sugar factory is a complex yet rewarding venture with the potential for high profitability. This report has outlined the essential aspects of starting a sugar factory, from market analysis to cost estimation and environmental responsibility. By following this guide, entrepreneurs can ensure a well-planned and sustainable sugar manufacturing operation.